A Deep Dive into Hollow Steel Tubular (HST) vs. Concrete-Filled Steel Tubular (CFST) Structures
- Bustan Fatma Warsi
- Aug 25, 2024
- 8 min read
Introduction
The world of modern construction is continually evolving, driven by the need for innovative, efficient, and sustainable building solutions. Among the most fascinating developments are tubular structures, which have become a cornerstone in the construction industry. Hollow Steel Tubular (HST) and Concrete-Filled Steel Tubular (CFST) structures are two pivotal types of tubular structures that are transforming how we build today (Fig.1).
HST structures are renowned for their versatility and strength, offering remarkable performance under compression, torsion, and bending [2]. Their sleek aesthetic, ease of maintenance, and ability to withstand impacts make them an attractive choice for a wide range of applications [3].
Meanwhile, CFST structures combine the strength of steel with the robust properties of concrete, delivering high energy dissipation and reduced construction time due to their unique design, which eliminates the need for formwork [4]. These two innovative technologies are reshaping the architectural landscape and construction industry, offering new possibilities for building stronger and more efficient structures.
Section 1: Understanding HST and CFST structures
Hollow Steel Tubular (HST) structures are cylindrical or rectangular steel sections known for their lightweight and efficient design (Fig. 2a) . These tubes offer a high strength-to-weight ratio, making them ideal for applications requiring strong yet flexible materials. Their hollow nature allows for easy installation of services like electrical wiring and plumbing, which makes them a popular choice in high-rise buildings, bridges, and towers.
Concrete-Filled Steel Tubular (CFST) structures consist of hollow steel tubes filled with concrete (Fig. 2b), combining the strengths of both materials. CFST members offer the rigidity and integrity of reinforced concrete structures with the ease of handling associated with steelwork [5]. The concrete core mitigates the buckling issues typical of thin-walled steel tubes, resulting in structures with increased load-bearing capacity and seismic resistance [6]. This makes CFSTs ideal for use in columns and beams in buildings and bridges, where their excellent structural integrity and fire resistance are highly valued [7].
Section 2: Head-to-Head Comparison
When comparing HST structures and CFST structures, each material offers distinct advantages and drawbacks, making them suitable for different applications.
Strength: HST structures are prized for their high tensile strength and lightweight nature, making them ideal for projects where weight is a crucial consideration. Their hollow design enables excellent performance in compression, torsion, and bending across multiple directions. However, HSTs can be susceptible to buckling under high loads (Fig. 3a), which may limit their use in certain heavy-duty applications [1].
CFST structures, in contrast, excel in load-bearing capacity due to the combination of steel and concrete [8]. The concrete core prevents or delays the buckling of the steel tube, providing enhanced structural integrity. This makes CFSTs particularly well-suited for high-rise buildings and bridges, where significant load-bearing capacity and seismic resistance are required (Fig. 3c,d). Fig. 3e,f demonstrate that the strength of CFST by itself is much greater than the combined strength of HST and reinforced concrete (RC).
Flexibility: HSTs offer greater design flexibility due to their lightweight and hollow nature, allowing for more innovative architectural designs (Fig. 4a,b). Their ease of construction and ability to be prefabricated offsite also contribute to faster project completion times.
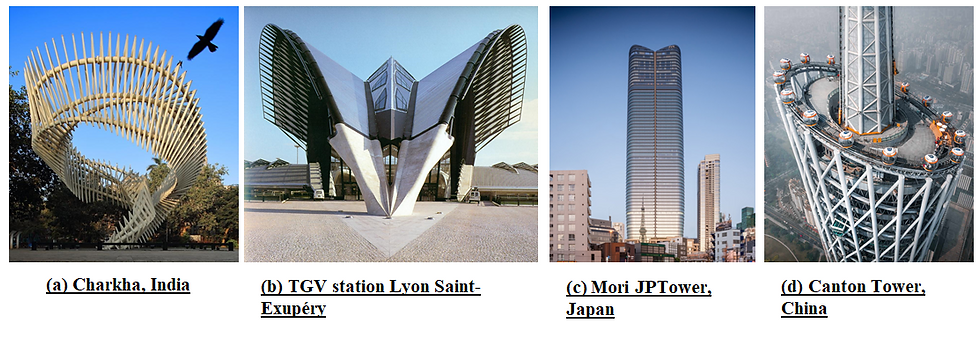
CFSTs, while more robust, are less flexible in terms of design due to the added weight and complexity of incorporating concrete [9]. However, this trade-off is often worthwhile for projects that prioritize structural strength and stability (Fig. 4c,d).
Cost: In terms of cost, HST structures are generally less expensive to produce and transport, thanks to their reduced material usage and lighter weight. However, their susceptibility to buckling can lead to higher long-term maintenance costs.
CFST structures may have higher initial costs due to the additional concrete and labor required, but their durability and low maintenance needs can result in cost savings over the lifespan of the structure, since steel tube serves as a formwork for casting while the concrete reduces the construction cost [10]. Additionally, the tube acts as a longitudinal and lateral reinforcement for the concrete core and no other reinforcement is needed, and the elimination of formwork in CFST construction can reduce overall construction time and expenses (Table 1).
Ultimately, the decision between HST and CFST structures is determined by the project's specific requirements, such as load capacity, design flexibility, and budget limitations. For a cost comparison, the prices of concrete steel and CFST are presented in Table 1 to provide an idea of the cost differences.
Table 1. Cost comparison of CFST vs HST
Material | Grade | Strength (MPa) | Area of steel tube/concrete/CFST (m2) | Cost (USD/m3) | Cost (USD/m) |
HST
| S275 | fy=275 | 0.02128 | 157 | |
S460 | fy=460 | 0.01064 | 115 | ||
S690 | fy=690 | 0.00665 | 94 | ||
Concrete | C50 | fck=50 | 0.09072 | 13 | |
C100 | fck=100 | 0.04536 | 9 | ||
C150 | fck=150 | 0.02835 | 15 | ||
CFST | S275_C50 | fy=275; fck=50 | 0.112 | 1522.92 | 170 |
S460_C100 | fy=460; fck=100 | 0.056 | 2228.39 | 124 | |
S690_C150 | fy=690; fck=150 | 0.035 | 3157.05 | 110 | |
![]() |
KEY:
fy=Yield strtength of steel tube;
fck= Characteristic compressive strength of concrete
Section 3: Sustainability Matters
The environmental impact of construction materials is a critical consideration in modern building practices. HST structures have the advantage of being lightweight, which can lead to reduced material usage and lower transportation emissions. Steel is also highly recyclable, aligning with sustainable practices that prioritize material reuse and waste reduction. However, the production of steel is energy-intensive, contributing significantly to carbon emissions.
In contrast, CFST structures benefit from the combination of steel and concrete, leveraging the strength and durability of both materials. The concrete used in CFST can incorporate industrial by-products like fly ash or slag, reducing the carbon footprint of cement production.
Additionally, the thermal mass of concrete can enhance energy efficiency in buildings by moderating indoor temperature fluctuations. While CFST structures require more materials, their durability and potential for using sustainable concrete mixes support their role in sustainable building practices. Fig. 5 depicts that CFST exhibits comparatively lower environmental impact value than HST.
If we will compare the CO2 emmission of concrete and steel, the production of 1 kg of concrete is associated with the emission of around 0.12 kg of CO2 into the atmosphere, while the production of 1 kg of steel emits 1.38 kg of CO2 . Both HST and CFST offer pathways to more sustainable construction, depending on the context and available materials.
But Since CFSTs combine both materials, so their overall emissions depend on the proportion of steel and concrete. The choice between CFST and HST affects the environmental impact, with CFST potentially having a lower carbon footprint due to concrete’s lower CO₂ emission.
Section 4: Future of HST and CFST Structures
The future of HST and CFST structures is promising, driven by technological advancements and the push for sustainable construction (Fig. 6a). Emerging trends include the integration of smart sensors into these structures for real-time monitoring, allowing for predictive maintenance and enhanced structural health management.
3D printing technology is also set to revolutionize the fabrication of modern structures, enabling the creation of complex designs that optimize material usage and performance [12]. This technology may facilitate the use of advanced materials, such as high-performance concrete and nano-reinforced steel, enhancing the architectural features (Fig. 7), strength and durability of CFST structures.
Sustainability remains a key focus, with innovations aimed at reducing the carbon footprint of construction materials. Research into low-carbon concrete and recycled steel is gaining momentum, promoting environmentally friendly practices. As modular and prefabricated construction methods gain popularity, HST and CFST structures will play a vital role in shaping resilient and sustainable infrastructure.
Conclusion
In conclusion, both HST and CFST structures have distinct advantages that make them valuable in modern construction. In the evolving landscape of construction, both HST and CFST structures play vital roles, meeting diverse needs such as the lighweight and versatile nature of HST and flexible, aesthetic, and sustainable, fire resistant nature of CFST, contributing to resilient, efficient, and sustainable built environments.
HST structures offer flexibility, ease of installation, and cost-effectiveness, while CFST structures provide superior load-bearing capacity and fire resistance.
Both materials contribute to sustainable building practices, with advancements in technology paving the way for enhanced performance and reduced environmental impact.
As construction techniques advance, the potential to combine HST and CFST materials could lead to innovative hybrid designs that harness the strengths of both, offering versatile and sustainable solutions for future infrastructure projects. Table 2 provides a detailed comparison of the different parameters of HST and CFST, highlighting their respective advantages and guiding informed design decisions.
Table 2. Comparison of HST vs CFST structures
Topics of Comparison | HST | CFST |
---|---|---|
Strength | Lightweight and high tensile strength. Suitable for various applications. | The combined strength of steel and concrete. Enhanced load-carrying capacity and ductility |
Flexibility | Versatile in design and aesthetics. | Outer steel tubes can be customized while maintaining structural integrity. |
Cost | Generally cost-effective due to efficient use of steel. | May have higher initial costs due to concrete filling, but long-term durability can offset this. |
Sustainability | Lower carbon footprint due to less concrete. | Can be designed with sustainable materials and optimized shapes. |
Future Use | Widely used in bridges, high-rise buildings, and architectural designs. | Evolving research and applications. Potential for innovative uses such as Hybrid Bridges and Viaducts, Urban Rooftop Gardens and Parks, and Seismic-Resilient Buildings |
![]() |
References:
[1] L.-H. Han, W. Li, and R. Bjorhovde, “Developments and advanced applications of concrete-filled steel tubular (CFST) structures: Members,” J Constr Steel Res, vol. 100, pp. 211–228, 2014, doi: https://doi.org/10.1016/j.jcsr.2014.04.016.
[2] P. Foraboschi, “Predictive Formulation for the Ultimate Combinations of Axial Force and Bending Moment Attainable by Steel Members,” International Journal of Steel Structures, vol. 20, no. 2, pp. 705–724, 2020, doi: 10.1007/s13296-020-00316-6.
[3] L. Gardner, “The use of stainless steel in structures,” Progress in Structural Engineering and Materials, vol. 7, pp. 45–55, Apr. 2005, doi: 10.1002/pse.190.
[4] D. Lam and L. Gardner, “Structural design of stainless steel concrete filled columns,” J Constr Steel Res, vol. 64, no. 11, pp. 1275–1282, 2008, doi: https://doi.org/10.1016/j.jcsr.2008.04.012.
[5] K. R. Harale and S. P. Kitture, “A Review on Developments in Concrete Filled Steel Tubular Columns (CFST),” IOSR Journal of Mechanical and Civil Engineering (IOSR-JMCE) e-ISSN, vol. 14, no. 4, pp. 1–04, doi: 10.9790/1684-1404040104.
[6] V. Gore and P. Kumbhar, “Performance of Concrete Filled Steel Tube (CFST) Section: A Review,” International Journal of Science and Research (IJSR), vol. 4, pp. 645–647, Nov. 2015.
[7] V. Kodur and J. Latour, “Experimental Studies on the Fire Resistance of Hollow Steel Columns Filled with High-Strength Concrete,” Jan. 2005, doi: 10.4224/20378403.
[8] M. L. Patton, S. B. F. Warsi, and D. Adak, “Experimental and numerical study on the structural behaviour of HST, RCC and CFST stub columns under pure axial compression,” Innovative Infrastructure Solutions, vol. 8, no. 2, Feb. 2023, doi: 10.1007/s41062-022-01025-1.
[9] K. B. Manikandan and C. Umarani, “Understandings on the Performance of Concrete-Filled Steel Tube with Different Kinds of Concrete Infill,” Advances in Civil Engineering, vol. 2021, no. 1, p. 6645757, Jan. 2021, doi: https://doi.org/10.1155/2021/6645757.
[10] J. R. Joseph and J. H. Henderson, “Concrete–filled steel tube truss girders—a state-of-the-art review,” Journal of Engineering and Applied Science, vol. 70, no. 1, p. 49, 2023, doi: 10.1186/s44147-023-00220-w.
[11] D. Chen, Y. Lu, X. Shi, and S. Gao, “Environmental-mechanical performance of steel-concrete composite columns under compression-bending loads based on life-cycle assessment,” J Constr Steel Res, vol. 219, p. 108750, 2024, doi: https://doi.org/10.1016/j.jcsr.2024.108750.
[12] S. B. F. Warsi, B. Panda, and P. Biswas, “Exploring fibre addition methods and mechanical properties of fibre-reinforced 3D printed concrete: A review,” Developments in the Built Environment, vol. 16, p. 100295, 2023, doi: https://doi.org/10.1016/j.dibe.2023.100295.