A Structural Review: The Shard | London designed by WSP
- Structures Insider
- Feb 13, 2023
- 4 min read
Updated: Dec 28, 2024

The name "The Shard" comes from the architect's description of the development as a "shard of glass" when it was being planned. The irregular nature of the site had an impact on its design.
The Shard, one of the most ambitious projects of the London South Bank regeneration, has become one of London's most iconic skyscrapers since its opening in July 2012 and with a height of 309.6 metres (1,016 feet), it is among the 100 highest structures in the world.
It is the fourth tallest building in Europe and the tallest building in the United Kingdom, but it is only the second tallest free-standing structure in the United Kingdom, having been surpassed by the Emley Moor transmitting station (330.4 m).
Irvine Sellar, the developer and joint owner, had the idea to build a "vertical city" that would house shops, offices, hotels, apartments, restaurants, and a public viewing gallery.
It is located at London Bridge, a busy transportation hub, where Sellar purchased Southwark Towers in 1998.
The Shard was designed by Italian architect Renzo Piano and built by Sellar Property Group in association with London Bridge Quarter Ltd.
As the structural engineer for The Shard, WSP was responsible for design, and the team was present on the job site for the entirety of its construction.
Key Details of the Project
Design and Construction
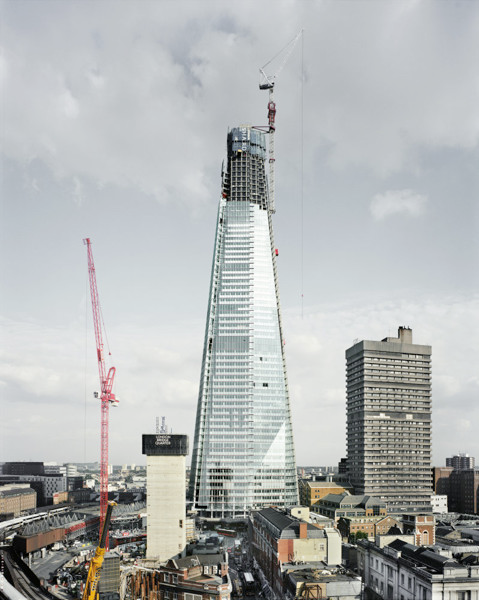
Delivering Europe's tallest tower in record time pushed structural engineers and contractors to rethink the fundamental principles of construction and employ new ways to build faster and taller than had previously been done in the UK.
To overcome the challenges of safely constructing a skyscraper in central London, adjacent to a major transportation hub, the team achieved a number of firsts, including the first top-down core, the UK's largest concrete pour, the first use of jump-lift construction, the world's first inclined hoist, and the first crane supported on a slipform.
Top-down construction
Top-down construction is a time-saving technique in which construction occurs from the ground level downwards. At the location, 500 mm x 500 mm steel columns were "plunged" from the ground level through empty pile bores into freshly poured concrete.
The slab was then cast directly on grade. After gaining strength, the slab was capable of propping the perimeter embedded walls and could be supported by the plunge columns, allowing excavation below the slab to proceed. This allowed the construction of the superstructure and basement to proceed simultaneously.
This technique made it possible to construct the first 23 storeys of the 72-story concrete core as well as a large portion of the surrounding tower before the basement had been completely excavated. This was needed because of the difficulty of constructing a skyscraper in a densely populated location near to a major transportation hub, and it helped to shorten the lengthy construction schedule by four months.
Foundation
Another difficulty with constructing modern skyscrapers in old towns is the possible presence of archaeological artefacts. The foundations of the Shard were also affected by the piles of Southwark Towers, a 26-story reinforced concrete building built in the 1970s. This structure had no basement and was supported by under-reamed piles embedded in London clay.
As their depth was only a few metres below the Shard's basement slab, they were not suitable to be reused as vertical support for the new skyscraper. Because it was not economically feasible to remove the existing piles, the new piles were constructed to fit between the original piles and their under-reams. A laser-guided drilling rig was utilised to surgically insert pilings among Victorian-era subsurface utilities and ancient archaeological artefacts.
Made ground | +4.7 m OD to 0.0 m OD |
River Terrace Gravel | 0.0 m OD to -6.0 m OD |
London Clay | -6.0 m OD to -27.0 m OD |
Lambeth Group Clay (cohesive soil) | -27.0 m OD to -39.0 m OD |
Lambeth Group Sand (granular soil) | -39.0 m OD to -45.0 m OD |
Thanet Sands | -45.0 m OD to -57.5 m OD |
Chalk | Below -57.5 m OD |
The ground conditions at the site were typical of those seen at construction sites located within the city, consisting of man-made ground above natural strata.
To withstand the very huge concentrated loads, 1.2 m and 1.5 m diameter rotary drilled piles were found at the top of the Thanet Sands.
About the Shard's unique ARCHITECTURE
Renzo flipped over his menu and started to sketch. What he drew in seconds is remarkably similar to The Shard today....
Continue Reading: Architectural Review of the Shard | London | Renzo Piano
Construction Materials
The distinctive tapered form consists of the following structures:
First 40 floors: Composite steel frame.
Up to the 60th floor: Post-tension concrete frame.
Up to the 72nd floor: Conventional reinforced concrete frame.
Spire to 87th floor: Pre-fabricated steel.
The use of concrete and steel improved the structure's efficiency. Post-tensioned concrete was better suited for the smaller spans higher up the building, saving 550 millimetres per level. In addition, ceiling space for services was improved by the use of uniform-depth steel beams acting in combination with concrete floor slabs. The structure contains 11,000 panes of glass and has a total surface area of 56,000 square metres (600,000 sq. ft).
The use of concrete in the building's core offered several advantages:
It provided damping at the top levels minimising the lateral acceleration and thus, controlling the building's swaying motion in the wind. This also removed the requirement for a tuned mass damper, freeing up additional residential space.
It allowed for shallower overall floor depths, allowing for an additional two floors within the total height of the building.
Prefabrication and preassembly of the 500-ton, 66-metre steel spire to reduce the dangers associated with working at such unprecedented height.
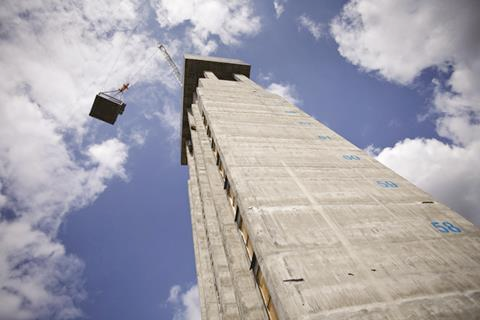