Robots to the Rescue
- Julianna Widlund
- Aug 16, 2022
- 5 min read
Updated: Nov 16, 2023

Could bots be the artificial sidekick the engineering industry needs?
Introduction
It is no secret that robots have slowly but surely been inserting their way into the lives of humans. Whether you have a Roomba clean your floors, an Alexa telling you what the weather is, or Siri setting your reminders, a robot has somehow become a part of your normal day-to-day.
Robots in Civil Engineering
In the civil engineering industry, drones are a type of robot that has "joined" the workforce so to speak. For those of you who are unfamiliar, a drone, by definition, is an unmanned aerial vehicle (UAV). Drones can range in size from something like a small plane to a child's toy. UAVs are a component of an unmanned aircraft system, which includes adding a ground-based controller and a system of communications with the UAV.
Most people who fly drones know they are an excellent tool for capturing aerial views, but did you know that another major use of drone technology is inspection and land surveying?
Civil and geotechnical engineers around the globe are now implementing drone surveying as part of the project planning process. Using an unmanned aerial vehicle for surveying purposes provides a quick and safe way to measure out large areas of land without risking human life by putting people on or near treacherous terrain. Engineers are even able to conduct surveying from a distance during rock blasting.
These unmanned flying machines can map the earth's surface with incredible precision and accuracy, so they're being used more frequently for surveying.
Another positive that comes with using drones is increased productivity.
Consistent efficiency is key to the success and growth of any business, and drone technology in construction is an excellent method of improving productivity. Having high-quality, visual information will allow project teams to better inform decision-making, leading to an overall improvement in productivity.
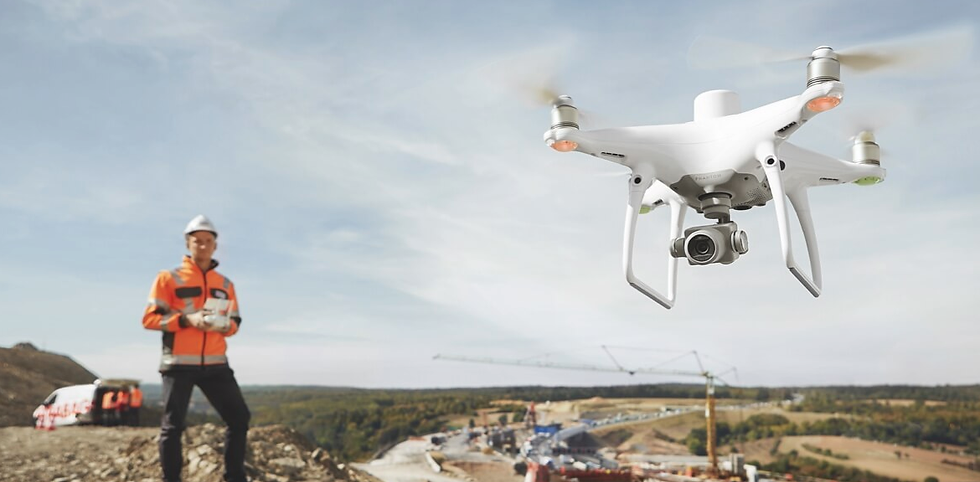
Another area in which drones improve productivity is freeing up time for people to work on different aspects of the project. This will free up resources for those who require a greater level of human interaction. Drones can investigate sites faster than humans can on foot. People can use that saved time working on tasks that require more of a human touch, such as finishing off details that would otherwise take longer to complete.
Staying under budget is essential to the success of any construction project. Everything must run according to plan, and keeping track of the current progress will ensure a smooth process and avoid delays. Drones can play a huge role in ensuring that projects stay on schedule and within budget. Aerial imagery allows engineers to see exactly where they are on the project site, and compare the initial survey maps to the current flyovers. This gives them a clear picture of what has already been completed, and what still needs work. Drone footage can also be used to save time and money by reducing the number of hours spent on site.
Sharing of Data
Lastly, access to shareable data is something drones have been improving upon. The engineers who use drones to capture images and video footage can now share it across the entire project. These images and videos help keep stakeholders informed about progress and allow them to see exactly what work is being completed.
Drones are also used to collect data that can be analyzed later. For example, if a contractor is working on an underground pipeline, they may send a drone into the ground to take photos and video footage. Later, these images and videos can be reviewed to determine whether any damage was caused during construction.
Other areas where drones can prove to be effective:
Site Reconnaissance
Roadway Assessment
Culvert/Bridge Inspections
Streambank/Steep Slope Access
Park and Open Space Aerial Imagery
Water Tank/Standpipe Inspection
Building/Roof Inspection
Treatment Plants
Orthophotography
Terrain Modeling
Construction Inspection
In addition to a little robot in the sky, there are efforts for a "swarm of mini robots" underground. Yes, a swarm. The underground excavation industry is exploring mini robots to replace the massive boring machines now in use.
For decades engineers seeking to build tunnels underground have to rely on huge tube-like machines armed with a terrifying array of cutting wheels at the front — "blades that eat dirt for breakfast." These behemoths, known as tunnel boring machines (TBMs) are costly and often custom built for each project. The TBM used to dig a path for London's newly opened Elizabeth line railway was custom built for that job. The machines deployed to dig the tunnels under the UK capital weighed over 1,000 tonnes each and cut tunnels over seven metres in diameter.
New tehnology in Tunnel Engineering
HyperTunnel, a British firm, however, has other plans. The company envisions a future where considerably small, half-cylinder-shaped robots that are around 3 meters long go through pre-drilled pipes underground. These pipes, which would have a diameter of around 250 millimeters (10 inches), would trace the outline of the proposed tunnel's walls.
Once inside, the bots would drill small holes into the surrounding dirt using a robotic arm equipped with a milling head, which would later be filled with concrete or another sturdy substance. In this manner, the framework of a new tunnel would be put together piece by piece.

“We’re talking about thousands of them,” says hyperTunnel’s director of engineering, Patrick Lane-Nott. “Much like an ant colony or a termite colony works in swarms.” — Wired
The tunneling experts who spoke to WIRED agreed that the industry is desperate for technological solutions to lower costs and increase efficiency. It can take years to design and build a TBM and then actually dig a tunnel. A new tunneling method would be revolutionary.
This new method would be like building a tunnel in reverse. "We put the tunnel in the ground — and then we dig the hole," says Lane-Nott. Once the structure has been built, the material filling the tunnel's chamber can be removed.
Obviously, this new method does not come without issues and concerns. None of these technologies have been able to perform at the scale they are needed for and the technology could still be years behind commercialization. It is nice to imagine a future where our technology is working for us and it is up to us as engineers to support this push forward.
References
Drones: Breakthrough Technology for the Civil Engineering Industry Drones are becoming more and more common in many sectors of the economy as they guarantee the fastest and most accurate…carrollengineering.com
9 ways technology is shifting the civil engineering industry Civil engineering is an ever-changing industry. With advancements in technology, we've seen the civil engineering field…www.usdredge.com
The Major Benefits Of Using Drones In Civil Engineering | The Drone Life In civil engineering, an effective plan and efficient process is everything. One technology that is growing in use in…thedronelifenj.com
Swarms of Mini Robots Could Dig the Tunnels of the Future The underground excavation industry is exploring mini robots, plasma torches, and superheated gas to replace the…www.wired.com